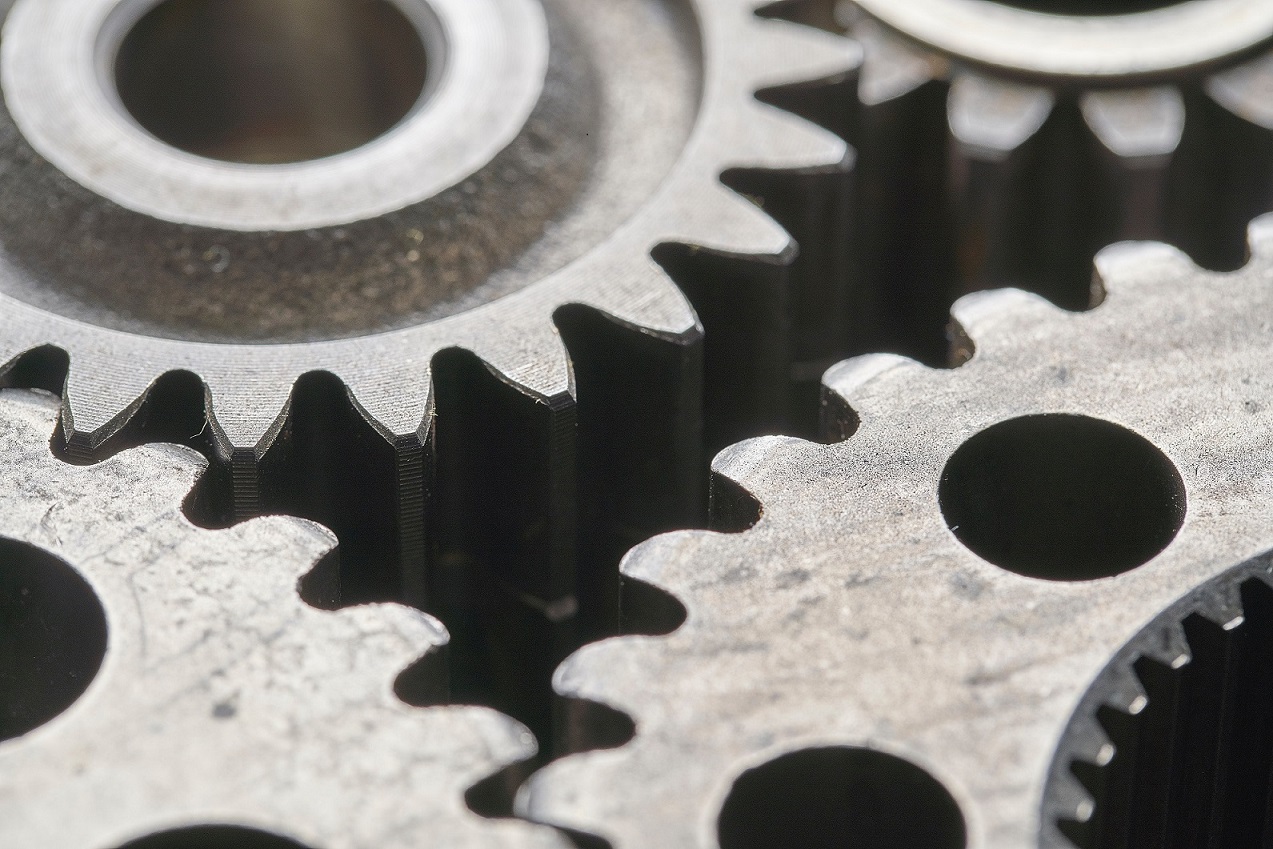
The MRP for Material Requirements Planning
The Material Requirements Planning or MRP is at the heart of the MRP method — Manufacturing Resource Planning. It allows to determine the proposed orders from the gross requirements in finished products determined with the MPS:
- launches in production
- or forecasted supplies
Indeed, it is from the bills of material* and the MPS (Master Production Schedule) or from the order book expressing the commercial needs of each product, that we will be able to calculate the dependent needs of each element, sub-assembly, raw material to be purchased or manufactured.
Of course, the planning horizon will take into account the purchasing and manufacturing lead times of the elements to be produced.
The MRP generally applies to both “mass” and “workshop” type productions.
Thus, the Material Requirement Planning will be used for the scheduling of any production. As long as standardized components are used in the manufacture of several products at identical or different BOM levels.
*It is the detailed description of all the components of a product and its conditions of use, it is the structured inventory of all the items that make up a product.
Note that, arborescent, the BOMs have several levels and must define the links between components. To be usable in a reliable MRP, bill of material descriptions must be complete and error-free. Indeed, any mistake will have repercussions:
- out of stock,
- increased production costs,
- Inaccurate material requirements planning…
To learn more about MRP — Material Requirement Planning, download the Professional Thesis — Specialized Master “Are SOP tools integrated with ERP?” of Thibaud Dilly
« Back to Glossary Index