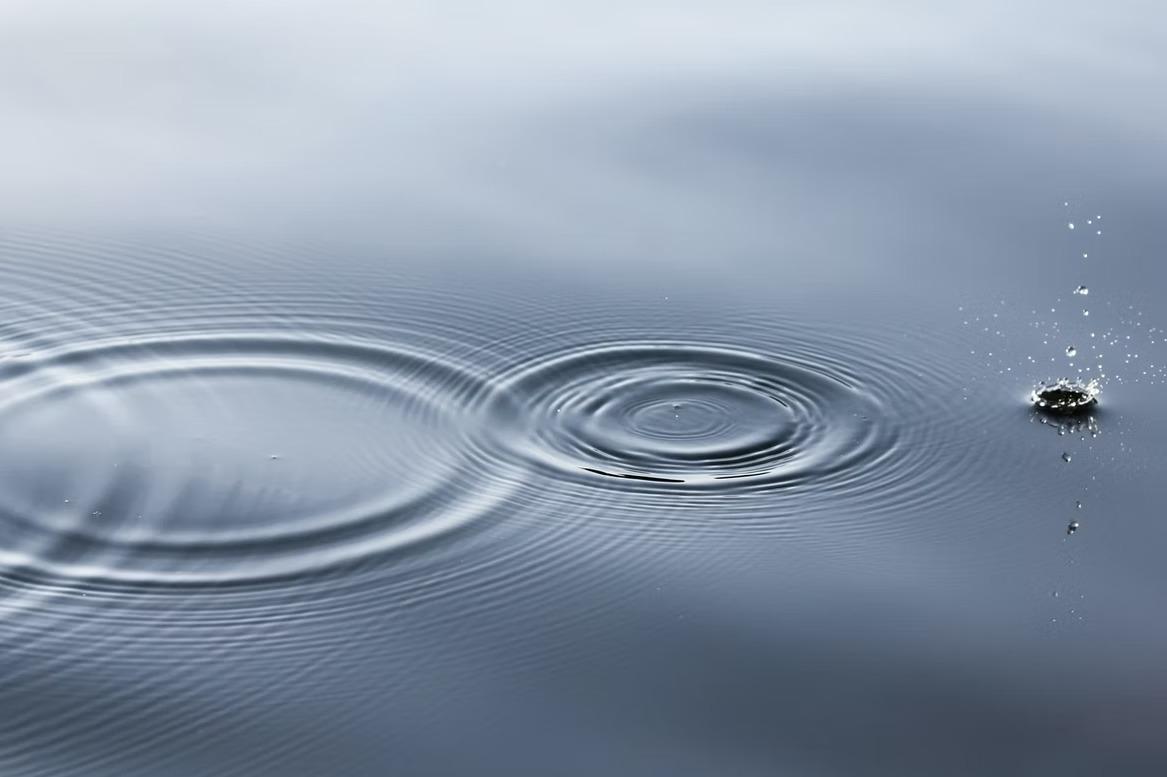
The supply chain is organized around multiple flows of materials, information, and finances. Their planning, management and control along the chain is essential to enable downstream customer service. As the supply chain is made up of multiple actors with different practices and regulations, this tends to increase the degree of uncertainty and dynamic behavior of the supply chain.
A good example of this dynamic is the rather explicit bullwhip effect — also known as amplification of demand variability.
What is the bullwhip effect?
In concrete terms, the APICS defines this effect as follows: ” The amplification of demand change up the supply chain is caused by a minor change down the chain. Inventories can then quickly go from being out of stock to being in surplus ” (Apics Dictionary, 2008).
The bullwhip effect results in either an increase in inventories when demand weakens, or a shortage when demand increases.
It generates excessive fluctuations in demand or storage points throughout the supply chain. This is confirmed by the APICS “This phenomenon is due to the cascade effect of orders ‘going up’ the chain and product transport delays ‘going down’ the chain”(Apics Dictionary, 2008).
Even a small change in consumer sales results in an increase in orders up the chain. This increase in orders increases the further up the supply chain you go (from the retailer’s orders to the manufacturer’s)… Orders causing an increase to an inventory build-up situation as already mentioned.
To maintain service rates, overstocking will occur. This overstocking eventually leads to a poor use of resources, a decrease in the profitability of the organization (decrease in WCR, increase in fixed assets in stock…).
This effect stems from the irrational behavior of the actors in the supply chain.
Some examples
In the last few years, there have been two significant events in irrational consumer behavior:
- first a rush on the toilet paper at the beginning of March 2019 due to a “panic buying” behavior
- and recently, the same situation is happening on oils in the first half of 2022
The increase in customer demand eventually creates a shortage or rationing when, without much change in consumer behavior, these products could be adequately supplied — at least initially.
It should be noted that a situation where supply contracts over a medium-term horizon can actually lead to a lack of product availability.
What are the root causes ?
Customer behavior is not the only culprit. The companies involved in the supply chain also have a role to play in amplifying the variation in demand.
Among the most common causes are:
- a lack of reliable information transmitted from one actor to another in the supply chain
- demand forecast adjustments (seasonality, trends…)
- grouped orders
- price fluctuation
- rationing and maintained scarcity
- the variability of the deadlines giving place to potential long lead time (materials, transport, production…)
- machines out of order, under maintenance or any other activity that impacts and limits production capacities
- promotional offers
Generally speaking, the more actors along the supply chain, the longer the whip and therefore the greater its amplitude.
Globalized, segmented and just-in-time chains with many specialized suppliers are weakened and more sensitive to the bullwhip effect.
Is the “firefighter mode” or reactive management, which consists in continuously taking corrective actions to manage emergencies and unforeseen events, with exceptional transport and other catch-up methods, sustainable? While these solutions may be viable in the short term, they tend to exacerbate the phenomenon and are costly.
How to reduce the bullwhip effect?
The sustainable solution proposed by APICS is: “The bullwhip effect can be eliminated by synchronizing the supply chain” (Apics Dictionary, 2008).
Therefore, some of the causes listed above can be easily countered by implementing the following measures:
- improve communication between players: partnerships, VMI (Vendor Management Inventory), EDI. The reliable and constant sharing of information between actors will allow everyone to adapt without under/over stocking.
- reduce or control the influence on demand: more stable prices, controlled actions and promotions or managed with an adapted software package
- size supplies: not only on the basis of “economic” lots and place constant and not exaggerated orders
- adjust the sales forecast to be as accurate as possible and be aware of their limitations
- not to maintain the shortage and not to ration the production
- to have a good dimensioning of the safety stock to avoid the double order
- Risk management to have contingency plans in case of extreme situations
- manage production capacities as precisely as possible with the MPS(Master Production Schedule)
- set up an S&OP (Sales & Operations Planning)
- place capacity, time or inventory buffers, paying attention to bottlenecks. Pool them when possible — pooling.
Bullwhip effect: which tools?
It is also possible to implement some tools from the Lean Manufacturing methodology. This will reorient the flows towards a demand-driven “pull” system that will provide flexibility and agility.
Also consider delayed differentiation and DDMRP. It explodes BOMs, which allows you to size and place buffers at strategic points while reducing lead times. In fact, the bullwhip effect is reduced.
It is good to specify that a well parameterized computer system, which takes into account all the parameters mentioned above will give good results exploitable for a good piloting of the organization.
Don’t be afraid of disruptions and trust your supply chain ecosystem.
« Back to Glossary Index