Qu’est-ce que la préparation de commande ?
La préparation de commande rassemble les activités de prélèvement des articles dans le stockage (plateforme, stock usine, magasins). Vient ensuite le regroupement des articles avant leur expédition au client, dans les quantités souhaitées par ce dernier.
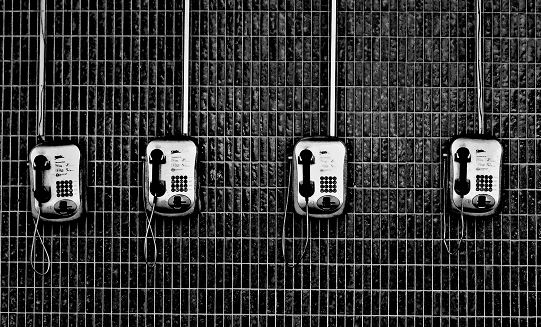
Cette opération cruciale et à valeur ajoutée non négligeable, est aujourd’hui au centre des préoccupations des entreprises. Les WMS – Warehouse Management System les aident dans leur recherche de productivité (nombre de lignes de commandes préparées par préparateur) et de fiabilité (% de lignes de commandes sans erreur (quantité ou référence article).
Les types de préparation de commande
Il existe différents types de préparation de commande (picking, éclatement, par commande, multi-commandes, positionnement du tri…), plusieurs modes (guidage vocal, radio,…). Et enfin, plusieurs types de regroupements avec eux-aussi plusieurs techniques sont disponibles.
Picking
- L’opérateur ou le préparateur de commandes se déplace jusqu’à l’emplacement de stockage pour prélever le produit et constituer la commande
- Mono-Commande Pick and pack : il prépare commande par commande (une seule commande à la fois sur l’ensemble des zones, ou une commande à la fois sur une zone donnée, complétée par un autre opérateur sur une autre zone) en posant les articles prélevés dans le colis
- Multi-commandes ou prélèvements groupés Pick then pack : plusieurs commandes prélevées en même temps (massification des prélèvements), avec une opération de tri au final pour composition du colis client
Dans les grosses structures de stockage, il est possible d’installer des convoyeurs munis de gares. Ils permettent de cantonner les préparateurs de commandes à des zones de dimensions restreintes et de leur proposer une préparation colis par colis. Le convoyeur arrête le colis dans les gares desservant les zones contenant un ou plusieurs articles à prélever. Une fois les articles disposés dans le colis, celui-ci reprend la file sur le convoyeur jusqu’à la dernière gare de prélèvement.
Avant expédition, un contrôle pondéral automatique évacue sur une voie de contrôle manuel, les colis dont le poids brut ne correspond pas au poids brut total théorique. Ce système piègera les erreurs de produit, les produits manquants… sauf si le poids total reste égal au poids théorique avec la marge de tolérance.
Ce contrôle est néanmoins le garant du taux faible d’erreur de préparation, et de la satisfaction du client.
Mise en place de convoyeurs et de systèmes automatiques
Il vous faudra en priorité disposer des bonnes données techniques de chacun des produits :
- Dimensions, soit Largeur, Hauteur et Profondeur, poids
- Caractéristiques spécifiques : densité, produit dangereux pour la bonne utilisation des zones de stockage et le calcul au plus juste des poids théoriques des colis seront renseignées
A noter : l’équipement de contrôle pourra aussi servir au renseignement des données des produits dans la fiche article.
Le système de convoyeur communément appelé transitique est relié au WMS par un système WCS – Warehouse Control System pour le pilotage des gares, de la vitesse, des arrêts.
Les colis peuvent être lancés en PICK and PACK avec le BL (pré-colisage). Seuls les articles présents dans l’entrepôt au moment du lancement du BL pourront être prélevés, ou lancés avec la commande. Tout article présent au moment de la préparation pourra être ajouté au colis (colisage en fin de préparation).
De plus, les systèmes peuvent définir la taille des cartons à utiliser selon les données des articles se trouvant sur la commande. Des armoires de stockage, des transstockeurs peuvent aussi compléter la transitique de l’entreprise. Ces équipements disposent généralement de leur propre WMS, interfaçable avec le WMS central.
- Éclatement : dès réception d’une commande fournisseur, celle-ci est éclatée sur différentes palettes, représentant chacune une commande d’un client.
Les types de guidage
- Par étiquette : le bon de préparation comporte autant d’étiquettes que de types articles à prélever. Les étiquettes reprennent N° colis, nom ou code client, N° commande, code emplacement ou adresse et code article à prélever. Ainsi, elles sont ordonnées selon l’ordre de prélèvement, et servent en sortie à la confection du BL.
- Par terminal et radio : un terminal portatif comprend l’ensemble des informations nécessaires pour le prélèvement (étiquettes reprennent N° colis, nom ou code client, N° commande, code emplacement ou adresse à prélever, code article ou non si prélèvement à l’emplacement uniquement). L’opérateur valide le prélèvement, soit manuellement, soit par lecture d’un code à barre (préparation radio). La validation du prélèvement déclenchera le prélèvement suivant.
- Par casque ou vocal : les informations nécessaires sont données à l’opérateur via un casque. Une fois le prélèvement fait, l’opérateur le confirme oralement pour passer au prélèvement suivant. Des codes détrompeurs sont demandés pour la vérification des informations de prélèvement. Ce mode est majoritaire aujourd’hui sur les grandes exploitations. Fiable, facile à mettre en œuvre (l’enregistrement de la voix du préparateur nécessite environ 30 minutes), il nécessite d’une formation légère.
- Par lumière de couleur ou pick to light : un système lumineux indique l’emplacement sur lequel prélever. Chacun des emplacements comprend aussi un afficheur qui donne la quantité à prélever. En outre, ce mode est adapté aux petites pièces (composants électriques, électroniques par exemple) stockées en tiroir ou alvéoles nombreux sur un espace réduit. Un bouton permet sur chaque emplacement de valider le prélèvement.
Dans une même entreprise, les différentes méthodes et modes peuvent être déployés sur différentes zones. En effet, un même entrepôt pourra être mécanisé partiellement : convoyeur ou armoires ou transstockeur. Et il disposera aussi de zones de prélèvements manuels pour des éléments gros gabarits par exemple.
« Back to Glossary Index